From grazing sheep to beautiful textiles
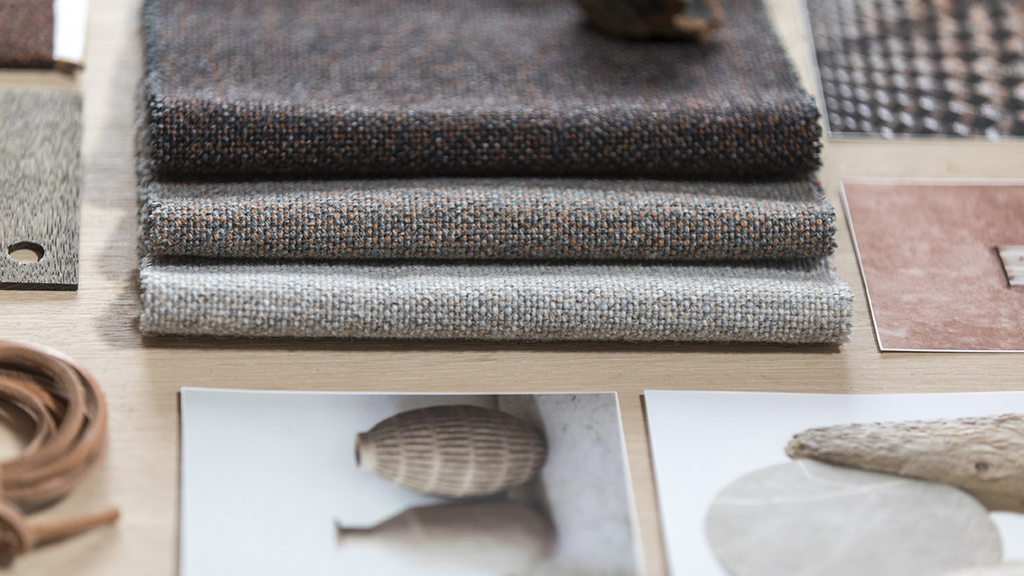
Gudbrandsdalens Uldvarefabrik is unique in that all processes take place under the same roof in the factory in Lillehammer. With full control at all stages of production, we have unique opportunities to develop and produce furniture and upholstery fabrics with the right design and technical properties.
The factory employs its own professionals who are responsible for design and product development. In addition, we often collaborate with external designers. Before a new textile sees the light of day, it must go through many processes. What starts with an idea on the drawing board must go through development, adaptation and testing. Finally, it passes through the eye of the needle and becomes a beautiful textile.
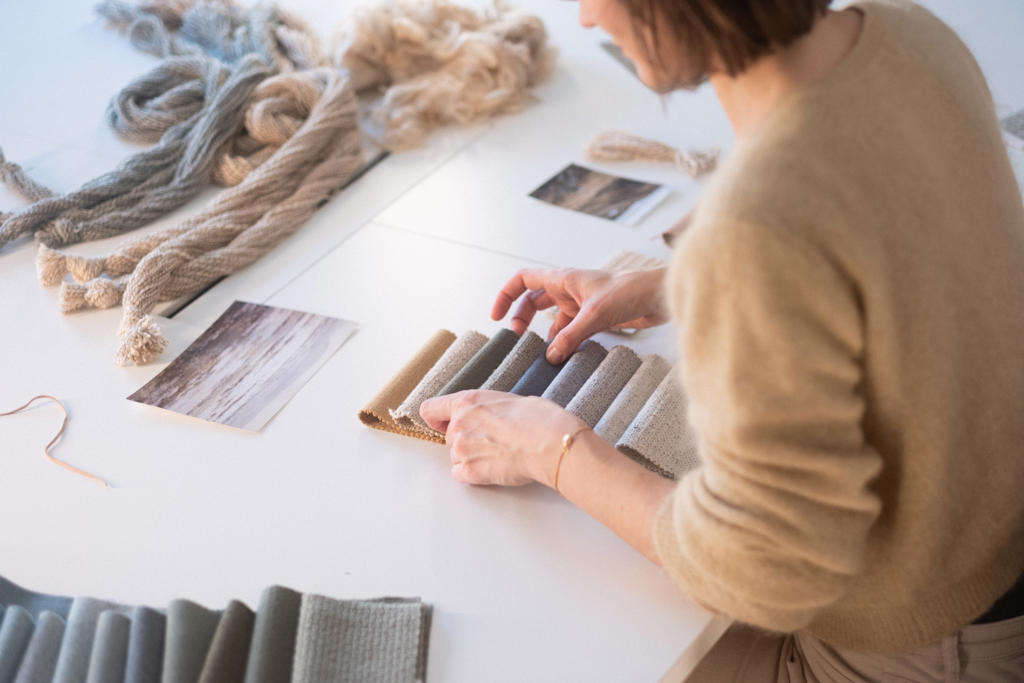
Textile design within the weaving trade is a subject that includes both design, technical binding construction, understanding of materials and real craftsmanship.
What is textile design?
Textile design within the weaving trade is a subject that includes both design, technical binding construction, understanding of materials and real craftsmanship. It is difficult to work with woven textiles without having insight into how the threads are tied together and function in a woven surface. Several elements come into play and contribute to a textile being unique, aesthetic and user-friendly: yarn structures and combinations, colours, how the threads meet in a construction and finishing. Gudbrandsdalens Uldvarefabrik has received the DOGA mark (formerly the Mark for Good Design) a total of 20 times for 23 products.
Design and product development
At Gudbrandsdalens Uldvarefabrik we have a separate team for design and product development. It consists of experts from all stages of production. The design team is led by Senior Designer & Product Developer Ragnhild Nordhagen, who is a real textile enthusiast from Bergen. Ragnhild has been with Gudbrandsdalens Uldvarefabrik since 2013. She had her first encounter with weaving at folk college as a 19-year-old and spent one year on the tailoring line at the Bergen Vocational School. She then trained in design and weaving, and has a master's in textile design from the University of Borås.
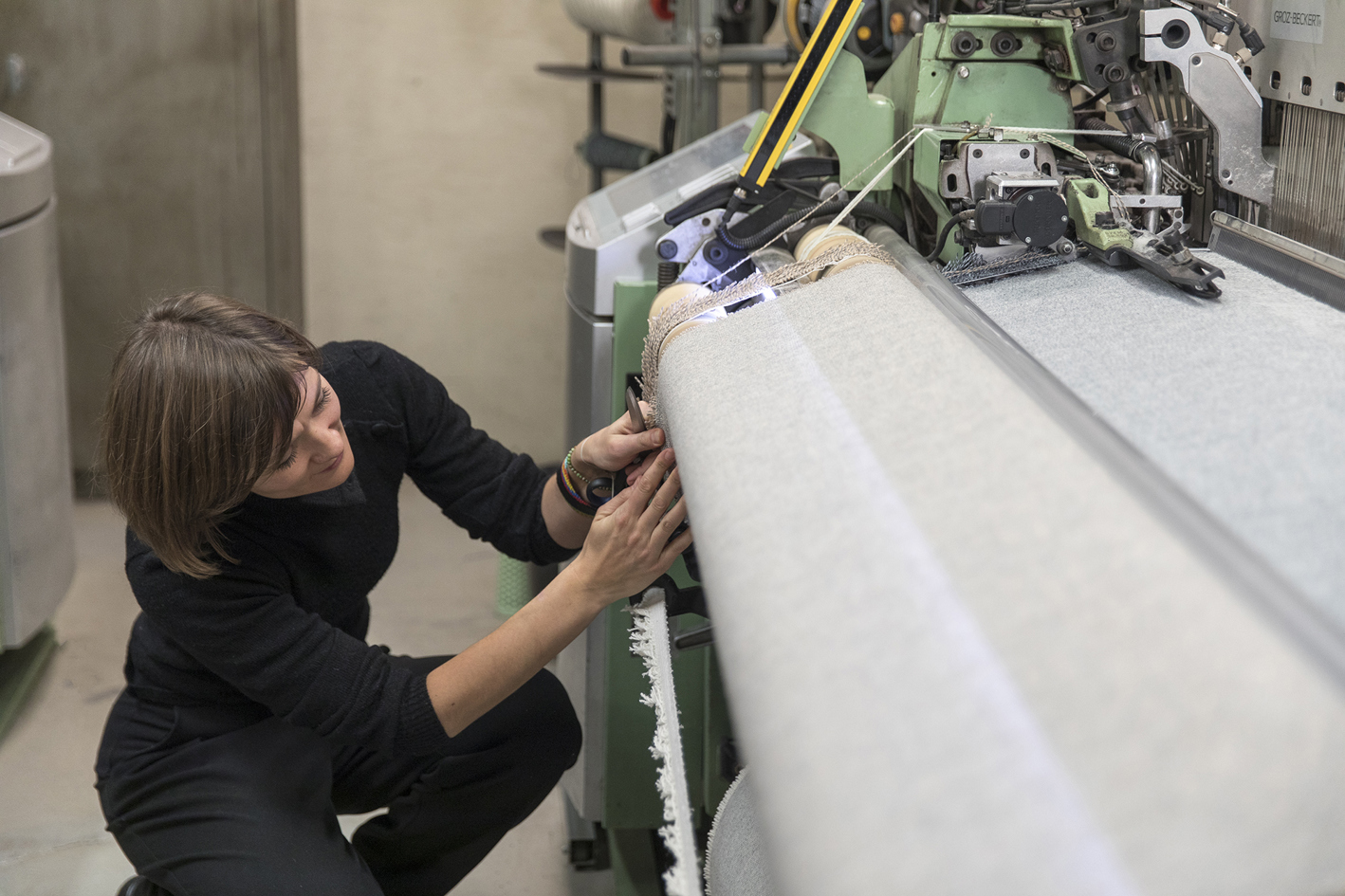
Each textile in GU's collection must be unique and stand out, and the whole must show a breadth of color and textures.
Ragnhild has always been extremely concerned with details in historical fashion and textiles. She is genuinely concerned that a textile should be "rich" - in the sense that it has natural materials, structure, details and colors that allow one to enjoy materiality and appearance.
In 2017, Gudbrandsdalens Uldvarefabrik and Ragnhild received the DOGA label for the furniture fabrics Sirdal, Suldal and Setesdal, which were developed in collaboration with Pernille Jensen Stoltze / Flokk.
We also work closely with Christiane Muller at Studio Müller van Tol in the Netherlands. Christiane has over 30 years' experience as a designer of surfaces, and works with several major players in the industry as a designer and art director. Our story with Christiane goes back to 2012, when she designed the Arkiv collection with inspiration from our archives.
In the spring of 2017, we re-initiated a collaboration with Christiane where we worked in-depth on developing a color and texture framework for how GU can work with colors and expanding its collection in the best possible way. We work on the basis that each textile has its own signature, with its own color series and identity. Each textile in GU's collection must be unique and stand out, and the whole must show a breadth of color and textures.
Dream team that creates wool magic
The team meets regularly to discuss the best possible development of our textiles. The weaving technician brings in expertise from the weaving mill and adjustments that are essential for the textile to be made, the color manager contributes with insight into colors and finishing, and the textile engineer with expertise in properties and testing. We are many wool experts at Gudbrandsdalens Uldvarefabrik, and love to geek out to the best results.
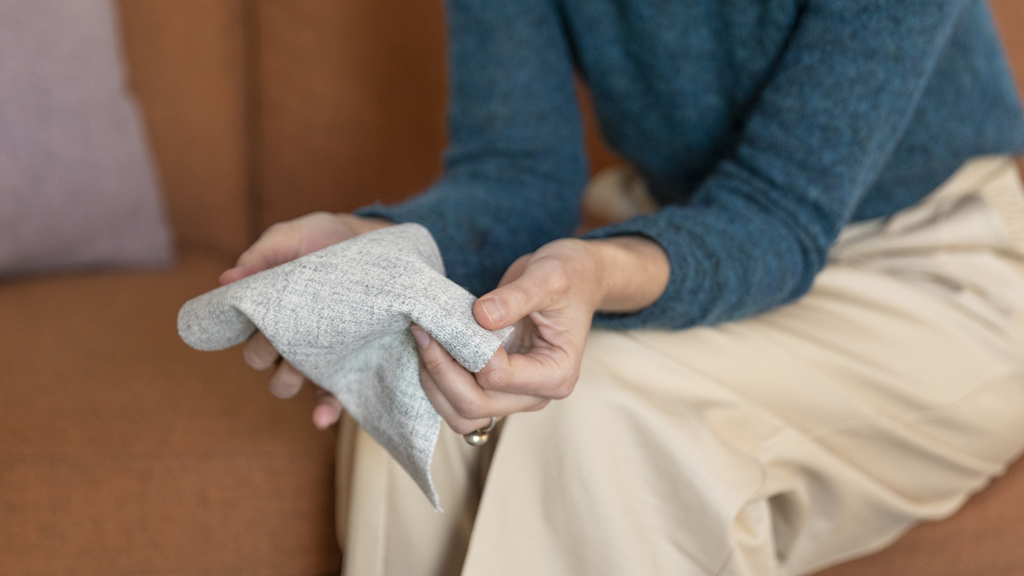
The design process
Inspiration and planning
When we start a design process, we often have a brief, a drawing/sketch, a picture or a piece of textile that shows what we want to achieve. Next, we have to look at how we can solve the material and technical issues. We build the textile from the ground up and work to ensure that the result is as we had intended from the start, or preferably even better than we could imagine. This is an incredibly exciting and extensive process with a lot of testing.
Patterns and colors
The pattern and bindings for the weave are constructed and drawn on a grid paper. The grid paper is a schematic representation of how the threads cross over and under each other in the fabric. Binding patterns and designs are also created digitally, and in the tool Nedgraphics, we can produce large, complex designs, add bindings and other information such as weft density, the order of different weft colors and create weave files that are read directly in the looms. We often develop new colors and the yarn or fabric is dyed in the dye shop. Often we have to do this several times to achieve the exact shade we want.
Yarn and weaving
The combination of yarn and weave creates its own structures and textures. You can have simple two-shaft bindings or complex jacquard patterns. There is always a small "aha!" element when the textile comes out of the loom - as it is difficult to 100% imagine a finished textile. Many textile designers work with hand weaving and make samples by hand, before the design can be taken further and tried out on the industrial looms.
At Gudbrandsdalens Uldvarefabrik, we are looking for a slightly "crafted" expression in our textiles. These are details that testify to the fact that these are natural materials and processes where craftsmanship plays a role. You do not get unison textiles where every meter is identical, but small irregularities that give character and value to the fabric because each wool fiber is unique.
Testing and certification
GU is one of the very few textile manufacturers in Europe with all processes under one roof. It provides very good and well-documented control and a far more transparent value chain. All our textiles are tested at external laboratories to achieve the correct certifications. These are often fire tests, tests on wear resistance, pilling/bumping, pliability, light fastness and environmental friendliness.
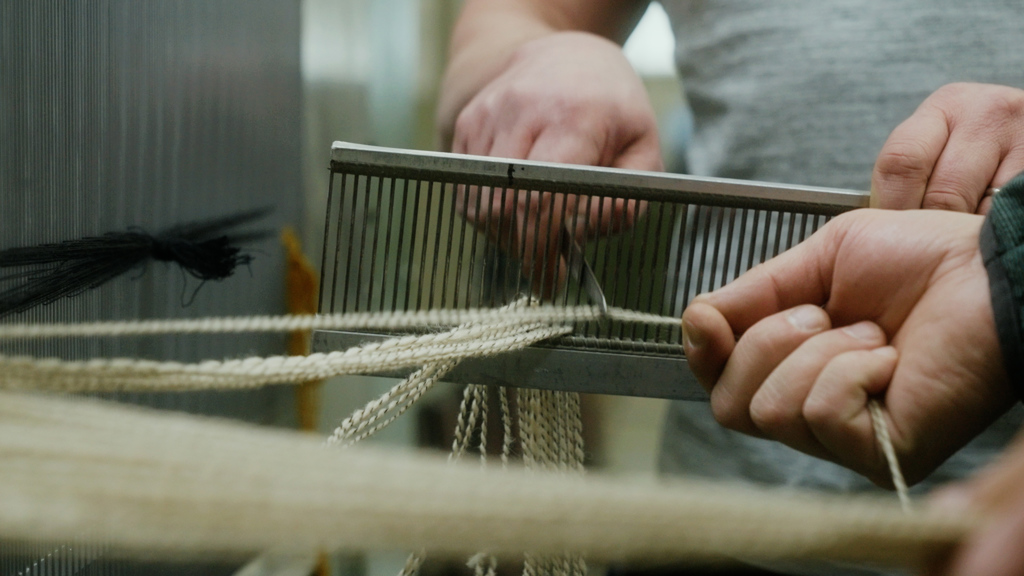
Collaboration with other designers
Over the years, we have worked with several designers such as:
- Pia Bjørnstad
- Anemone Wille Vage
- Per Bjørnsen
- Merete Haabeth Serrano
- Nanna Ditzel
- Anderssen&Voll
- Heidi Helland-Hansen
- Kari Skogstad
- Lotta Koehler
- Sari Syväluoma
- Pernille Jensen Stoltze
etc.
We also work closely with many of our large customers on design. We always work based on what is in our DNA and we stay true to our background. This means that we always use wool and that we always produce high quality. Everything we create from new materials must be within this framework. We have to think about what is relevant in the times we live in, what is relevant for our customers and what is relevant for our collection. Our task is to create modern and exciting textiles within these frameworks
When designing textiles for industrial production, it is important to have a system for what the various yarns, bindings and machines can do, and try to challenge this. This involves a lot of analysis: of what we have done before and whether we can do something in a new way, which machines we have that are suitable, and finishing touches that emphasize the look and grip we are looking for.
A trip to the archive
We can also use our huge archive of old fabrics, learn from experience, recreate. It is important to always analyze experiences: what works, what doesn't work and why?
Product development also includes analysis of old fabrics, how we recreate textiles with very specific requirements for appearance, grip and fall. There are many experts in the sewing rooms who give invaluable input to achieve the best quality.
Here we show how we construct and show a bond in the tissue. As you can see, the bonds are drawn on a grid paper. The grid paper becomes a schematic representation of how the threads cross over and under each other in the fabric. When a route is drawn, this means that a warp thread (the thread system lengthwise in the fabric) crosses over one weft (the thread system across the fabric). Here is the simplest binding called "Two-Shaft"
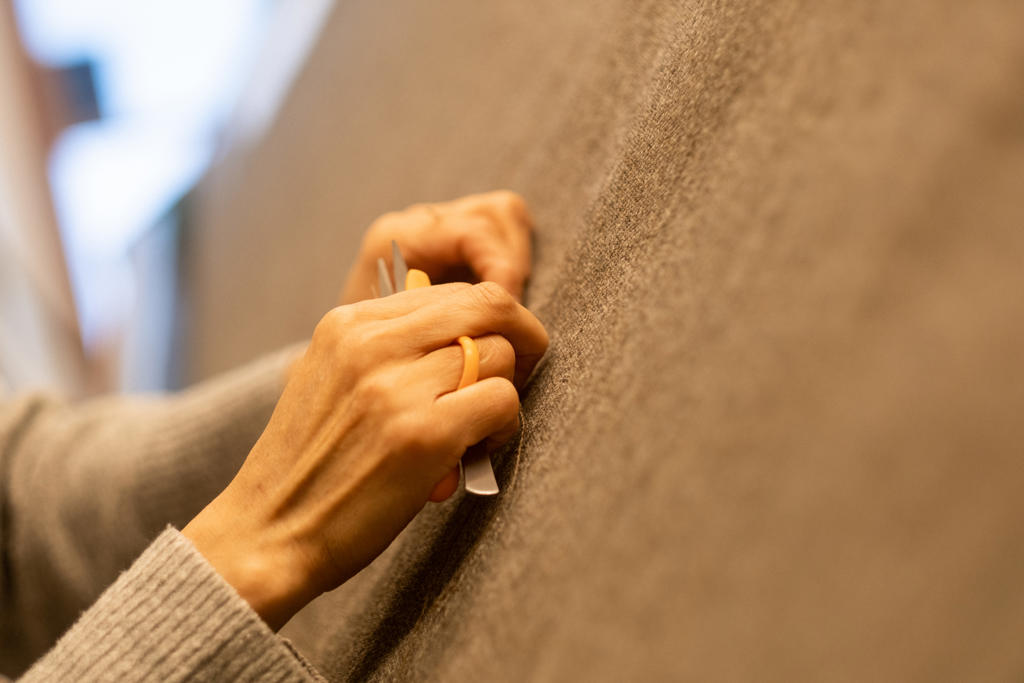
In synthetic fabrics, "bumps", also called pilling, are often formed due to static electricity.
Technical characteristics
Wear resistance (Martindale)
The wear resistance of an upholstery fabric is measured using a Martindale tester. This is the measurement of the number of rotations of the fabric against a standard cloth. The number of rotations when two thread breaks occur is given as a value to describe the wear characteristics of the fabric. All our textiles in the collection have a durability of over 50,000 rotations. In addition, some textiles have even more. These are often those that are used in public environments and that require very high wear resistance, such as cinemas and trains.
Pilling
In synthetic fabrics, "bumps", also called pilling, are often formed due to static electricity. Wool has a natural moisture level of 15%. This means that under normal conditions it will not charge statically and, as a rule, will therefore not nudge either. Nupping / pilling is tested by rotating the fabric against a standard cloth on the Martindale tester. Pilling is given on a scale from 1-5, where 5 is the best.
Light fastness
By exposing the textile to a light source at a certain temperature, it is checked how it retains its color when exposed to light, especially sunlight. Poor lightfastness often manifests itself as bleaching (fading) of colored textiles. The degree of fading is then evaluated, which is given on a scale of 1-8, with 8 being the best. All our textiles have light fastness between 5 and 7, which is considered to be a high level.
Color fastness
Color fastness is a measure of how much the color of a textile fabric changes when it is exposed to light, water, washing, sweat, rubbing or other stresses. The degree of color change is assessed using standardized test methods.
Resistance to rubbing
Resistance to rubbing expresses how much color is transferred or spilled onto a white fabric against which the fabric sample is rubbed. We can test both dry and wet resistance to rubbing. The results are given on a scale from 1-5, where 5 is the best.
Flame Resistance
Tekstil av ull er naturlig flammehemmende. Ull har vanskelig for å antenne og brenner som regel ikke, men forkuller. Brann i kraftige, tykke ullstoffer slokker som oftest av seg selv. Brennbarheten til et stoff testes ved hjelp av en sigarett- og fyrstikktest og det som kalles for en krybbetest.